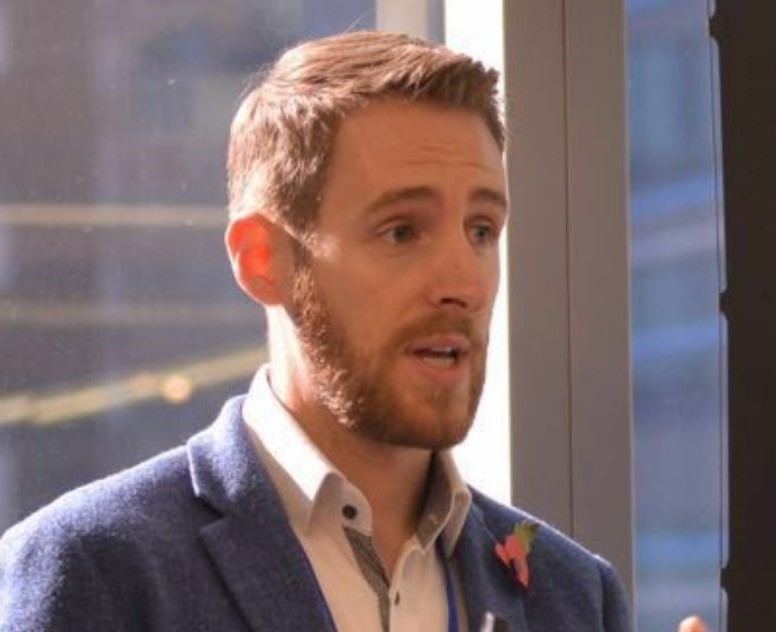
Jan 28, 2020 Asher Balkin interviews Adam Johns, Cathay Pacific Airways Safety Risk Manager
Adam Johns, based in Hong Kong, is helping Cathay Pacific Airways move from a traditional risk perspective to including a Safety II and Resilience Engineering view.
Asher Balkin is a Safety Researcher at the Ohio State University Cognitive Systems Lab
Asher: How did you learn about Resilience Engineering?
Adam: It’s been very organic, about 5 or 6 years ago I started to look beyond aviation to learn how to innovate in safety management. Aviation often gets held up as a panacea of doing safety very well and, while that’s true, aviation tends to look within itself for answers on how to improve. I read blogs and papers, mostly in the occupational health and safety space out of Australia then discovered the Eurocontrol papers on Safety II and systems thinking, it snowballed from there to work by Sidney Dekker, Erik Hollnagel, and David Woods. Essentially trying to think how we could implement these concepts in an airline environment.
Asher: You mentioned aviation looks within itself, this is particularly true of disciplines who do it well. “We are really good at this, why would I look into areas where they’re potentially not as good at this?”
Adam: Aviation had to get to level of safety that it has due to a societal expectation: 300 people dying in a single plane crash is huge news for days compared to 300 people dying in 300 surgical events individually. It isn’t going to make the news on the same scale. Aviation had to develop safety performance to the level it has now out of necessity. But look at the way aviation is going in terms of growth and experiencing exponential change with new technology. If we keep doing what we’ve always done, then we’re probably going to start falling backwards.
Asher: How has Resilience Engineering thinking impacted aviation?
Adam: We are still at the early stages. I’m only aware of a small number of other airlines who are trying to push into this space. Something needs to be done to take us to next level.
Asher: When organizations start to move to Safety II or Resilience Engineering, there’s often a concern that it may be too soft or not standardized enough. Did you experience this?
Adam: No. There was some initial skepticism but once people understood the basics, and they see the simple logic of learning from normal operations, it makes sense. It’s taken 2 to 3 years to get to this point of socializing Safety II but there was no resistance. People are now looking for more detail and asking “what do Safety II and Resilience Engineering look like in practice?”
Asher: That is a fair question!
Adam: In a Safety I perspective, safety and productivity are seen as opposing forces but if we apply Safety II ideas, we see safety and productivity as complimentary so we focus on trying to improve work. Safety and productivity both gain; we focus on trying to improve performance as a whole.
Asher: Has the industry being so heavily regulated confined the space you can explore?
Adam: If you go back 20 years, it would have been more difficult. Now aviation is moving to a risk and performance-based regulatory regime, led by the International Civil Aviation Organization. Taking this regulatory philosophy, as long as we achieve outcomes put forward by regulator, it’s up to us to figure how to do that. As long as we meet traditional requirements, there’s nothing stopping us from going beyond that.
An example of where Resilience Engineering has existed for quite some time is looking at normal work as part of Line Operations Safety Audits (LOSA): pilots ride in the jump seat and record normal operations against a template.
Within our training and checking environment, we added “clarify” to their process to probe local rational: observe, record, clarify , classify, and evaluate. When training captains observe performance, they use clarify to try to make sense of why a trainee did what they did. We are giving training captains a vocabulary of how to record performance to enable the mining of resilient performance.
Asher: You mentioned a disconnect between performance and risk, how do we discuss the relationship between risk and resilience and adaption?
Adam: Our focus is currently on flight operations with pilots; we know adaptation has to go on all the time. Workers are masters of blue line; they understand how work has to be done. Now we are asking: what is the adaptation? Is it safe or unsafe? Are we drifting in a good or a bad direction? Using this knowledge to understand the real risks in our organization. Are these adaptations helping us achieve a successful outcome and keep us safe or the opposite?
Asher: How did you come into your current role in safety?
Adam: I completed an aviation degree in the UK which involved getting my private pilot license – always wanted to be a pilot. My thesis was automation on the flight deck so then decided I wanted to get into safety instead. I worked for a company that provides flight data solutions to airlines then moved to work for an airline in the UK, the UK regulator, and now Cathay. I started in safety analysis roles but now focus more on proactive risk management of operational changes.
Asher: What’s next for Resilience Engineering in aviation?
Adam: We are focusing on the way we investigate: not just looking at accidents. Airlines have events all the time, most of them with little or no consequence, but they are still events the airline doesn’t want to happen. What we know is it’s the crew’s resilience that prevents that event from leading to a more significant consequence. We are introducing the Learning Review concept (Ivan Pupulidy, see his TedX talk) focusing on what went right and why it made sense for people to do what they did. This will get us to the next level of performance.
(Operational learning reviews are used in by the US Forest Service).
Asher: One fascinating thing about Resilience Engineering principles is that when deployed, we find that front line folks (sharp end) in a hospital, on a flight deck, or at a worksite are often taking actions that demonstrate much higher levels of resilience than we’d expect and much higher levels than they would even describe themselves. They say “Of course this is how I get the work done.” Is this something you’ve observed or is there more awareness of resilient behaviors?
Adam: Last year, we delivered a presentation on Safety II and resilience to our training capatins, and within that we asked them to write down everything that happened on their last flight that influenced performance – performance shaping factors – things like they were fatigued or dealing with inexperienced crew or had technical issues on the aircraft; they wrote down dozens of things. We asked “how many of those things did you record on your safety report?” No hands go up. That was a window into their world: they are dealing with these challenging aspects that influence performance every single time they go flying. These factors aren’t reported because they think, “That’s just normal; that’s what we deal with every day.” This is the tip of the iceberg in really learning from and understanding normal performance.
Asher: Have you made progress getting front line folks to realize how unique this is and move those kinds of insights up the ladder?
Adam: Yes, quite a few light bulbs went off amongst the roughly 300 pilots in a number of workshops. We are starting to see more reports come in from pilots on events they wouldn’t normally report and are getting better quality reports too. Although we haven’t provided the language we want to use to describe resilient performance yet, we are getting more detail and people are writing what they learned as a result of being involved in the event.
Asher: Far more has been written on a Safety II approach but not lot written yet on adding Resilience Engineering to a Safety II style program, how do you merge Resilience Engineering principles into Safety II program?
Adam: Start with language. Last year we presented concepts related to Safety II and resilience at each monthly safety meeting such as: complicated / complex systems, work as done / work as imagined, trade-offs, performance variability, local rationality. Using the principle that Words create worlds. We are aligning learning from normal work and how people make sense of what they do. We are implementing resilience by identifying resilient strategies and behaviors that people delivered during each event; with the language of “anticipate, monitor, respond, and learn” being integrated into how we monitor safety performance on the front line.
Asher: The language can be daunting, has this been a difficult barrier to overcome?
Adam: It’s not been as hard as expected. After we presented concepts “work as done” and “work as imagined”; the following month people were using the language. As a whole it could be quite daunting but if you break the concepts down into constituent parts around systems thinking and resilience, people can understand what you are trying to do. If you bombard people with all the language, all at once, it’s hard. Serve in a bite size way. One month we focussed on tradeoffs and talked about tradeoffs in a really simple way. The language seeps naturally into an organization and everybody starts talking about tradeoffs!
Asher: Early on folks decide that have to make the tradeoff to focus less on safety I and more on safety II. Do you have advice for getting started?
Adam: Don’t ignore the stuff you currently look at, incidents and near misses. Those still need to be looked at and learned from but you need to learn from them in a different way. Instead of focusing on what went wrong and looking at the human as a problem, focus on what went right as well and so much more learning can be achieved by doing that. Really understanding why it made sense for people to do what they did. Safety II includes Safety I, it’s just a different way of looking at what you already investigate. You don’t have to look at everything if your resources are limited. You don’t have to go out and observe normal work and look for extraordinary performance. You can just look at what you already look at in a different way.